The Remotion team developed Icarus in 2017 to refurbish conductors on one of the North Sea platforms. Primarily, the platform operator planned to conduct the work over the three years with rope access technicians performing necessary tasks during summertime. Meantime, Icarus robot completed the surface preparation in six weeks, illustrating the enormous efficiency potential of the robotic surface treatment.
The technology adheres to the offshore standards NORSOK Z-015 is ATEX Zone 02 approved. In 2019 and 2020, Icarus worked on jacket structures at Oseberg field in the North Sea.
In 2021 Remotion engineers upgraded the robot to perform a vacuum collection of debris. Soonafter, Icarus performed a conductor campaign at Sleipner A platform in the North Sea.
Unlike other Remotion models, Icarus uses non-magnetic, friction-based traction. A 4-point subsea clamp-inspired mechanism and a structure with a spring-loaded clamping act against the pipe. Electric servo motor drive on all 16 wheels gives the robot maximum friction. It is a lightweight machine which can be adapted to various pipe sizes within the range of 20 to 36-inch outer diameter. For larger pipes, a custom-designed robot is available on request.
Installation under the platform deck requires access technicians’ assistance. Once installed, the robot is operated in semi-autonomous mode from a remote control and monitored from a top-side control cabinet.
Icarus v1 on jacket structure

Icarus robot carries a circular 360º reach actuator carrying various cleaning and inspection tools, including UHP and HP blasting nozzles, a vacuum collector for debris, wrapping, cameras, NDT equipment and other sensors.
Icarus v2 offshore wrapping operation
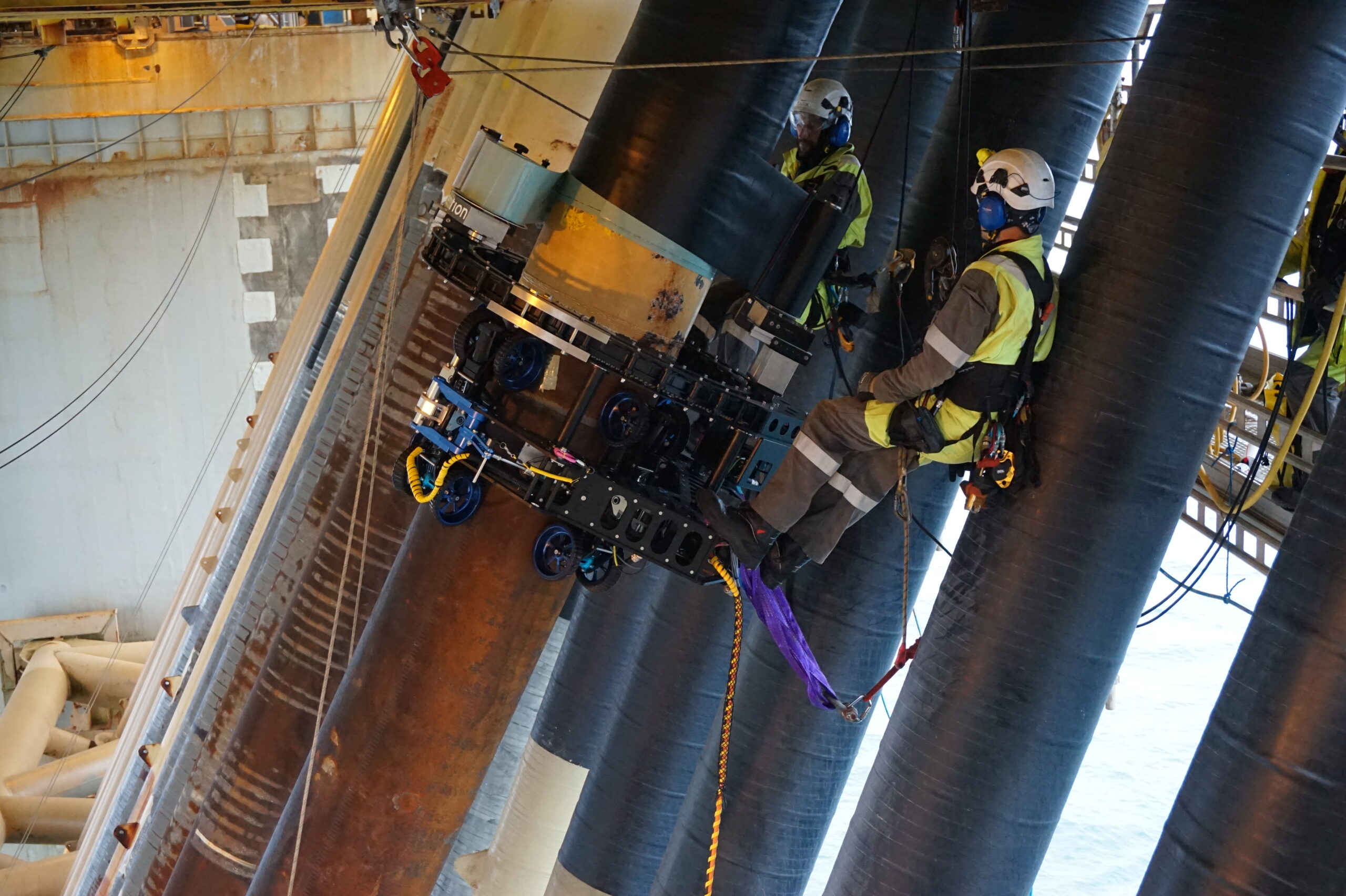
Icarus v2 with wrapping tool

See Icarus in action: