Goliath is our largest and most capable magnetic robot. It was our first design and proof-of-concept accomplished in 2014. Since then, the technology has been thoroughly tested and has proven its reliability in real-life working conditions.
Goliath is a hydraulicly powered vehicle with an on-board 8kW hydraulic power unit and a valve pack. It presents a very stable tool platform, capable of carrying and operating a broad spectrum wide of loads, including standard ROV tooling.
The robot is equipped with four patented Remotion magnetic belt drive units ensuring a magnetic traction force of up to 3,200 kg. The machine is designed to carry a high payload along steel hulls and structures in the splash zone. Because of its low height and a height open structure design, the hydrodynamic drag and added mass effect are significantly reduced.
The technology has broken its capacity record operating in 5.7m Hs wave conditions.
Goliath capabilities are consistently applied in the installation of cofferdams for sea chest blinding or hull crack repairs where the robot can carry a 3,000mm-wide cofferdam in front, or an outer diameter of 1,300mm-wide cofferdam underneath the main frame.
Linear tools in front of the vehicle include non-destructive technology (NDT) sensors, mechanical tools, cleaning accessories and other gears useful in such operations. These instruments can include and operate an extendable linear tool that can reach a 4000mm width.
The robot features an advanced Emergency Quick Release System (EQD) to ensure the machine can be detached and recovered under any conditions if the communication gets lost: he EQD system will automatically activate itself after overreaching a preset limit.
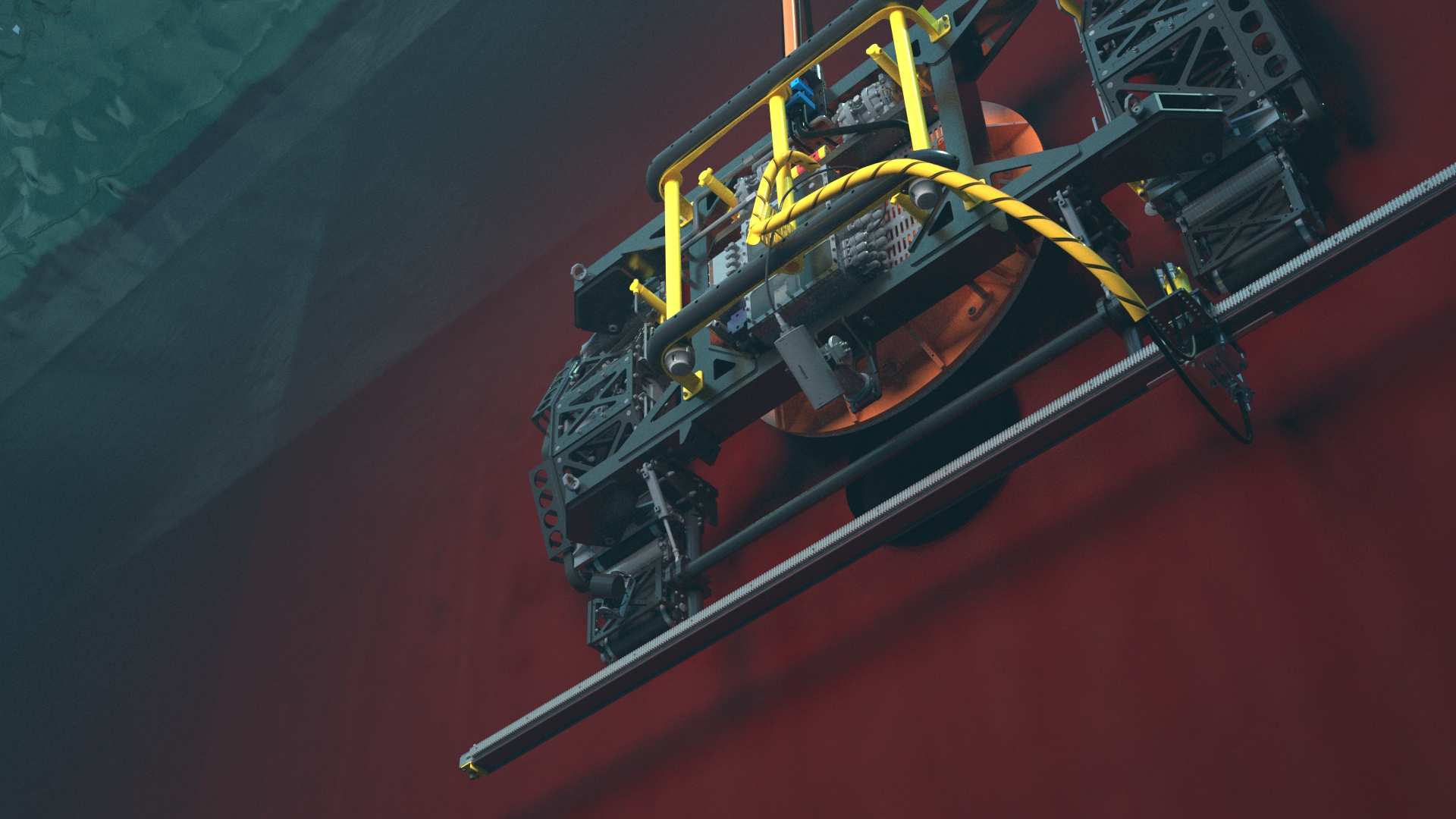
Goliath is typically lifted to the hull with a crane. The system comes with a transportation and deployment frame that can tilt the robot from a horizontal to a vertical position to ease the machine deployment and recovery. A running latch is used to connect and disconnect the crane hook.
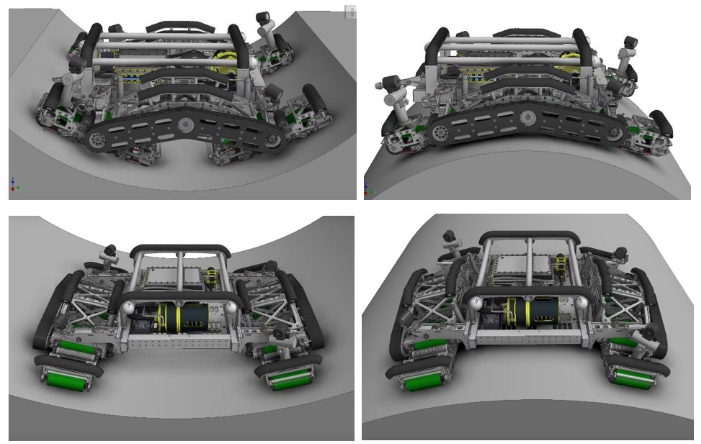
The Goliath compact package contains the robot, a 14’ control container, a safety winch and an umbilical winch. Despite its larger footprint, the smart drive unit can tackle various geometries in a radius down to 1,500mm. Such smart design allows Goliath to be used on large pipes on both internal and external diameter.
The robot is predominantly used for hull repairs, where it employs cleaning tools, a grinding machine and a cofferdam simultaneously. It can also perform a non-destructive ultrasonic inspection. Moreover, the machine can operate several Schilling Orion manipulator arms and act as a machining center. The concept was elaborated for fairleads and bilge keel repairs.
See Goliath in operation: