The largest differences between offshore units (FPSOs and FSOs) and conventional tankers are normally that offshore units:
- Are continuously loading and discharging in a variety of sea states.
- Have more global load cycles.
- Are weathervaning, meaning that the bow is constantly pointing towards the dominant weather.
- Have no possibilities to avoid severe sea states.
- Have a discontinuity on the bottom and/or main deck due to a moonpool.
- Have large loads that are transferred from the topside, the mooring system, cranes and the flare to the hull girder.
- Need repair work in tanks normally to be done in situ in unfavourable conditions, such as humid conditions and poor access.
- Are normally designed based on site specific wave statistics with a 100-year return period, while tankers are normally designed for the North Atlantic wave statistics based on a 25-year return period.
These differences may cause cracks at different locations for offshore units compared to conventional tankers. Petroleum Safety Authority Norway did a study of 17 units in the period between 2000 and 219, total 494 cracks were reported on these units.
The reparation of these damages is critical for the integrity of the structure, and it requires a certified, full penetration weld under controlled and safe conditions. Due to the harsh offshore environment and the unfavourable location of these cracks when found in the hull shell plates below the waterline, the reparation can require that the vessel is moved to a drydock resulting in that the production is shut down causing a tremendous economic loss for the operator. Minor cracks can be repaired with traditional methods like cofferdams installed by divers or ROVs offshore, but these operations require weather conditions that rarely are present offshore and in addition significant support and auxiliary systems like support vessels.
Remotion crack repair technology makes it possible to repair these hull cracks offshore, even under extreme conditions, while the production of the vessel is uninterrupted and with a small equipment spread and few personnel onboard the unit.
Our engineering team together with the skilled experience from our operators has developed a method which ensures that the area of the crack is properly sealed and kept dry from the outside of the hull, while welders can work safely and repair the damage from inside of the hull
To achieve this, we developed our advanced cofferdam system and installation method by our M-ROVs.
Our cofferdam offers:
- High temperature seals (270oC), which allow the pre-heating of the cracked area
- Double barrier; surrounding the welding chamber there is a secondary seal and vacuum chamber for increased safety
- Constant atmospheric pressure in the welding chamber
- Welding gas can be circulated inside the welding chamber
- Visual control of the welding chamber by HD cameras and lights from subsea
- Water ingress sensor in the welding chamber
- Temperature sensor in the welding chamber
- Pressure sensor in both the welding and the secondary vacuum chamber
- Remote controlled valve pack to control the drain and vacuum lines.
- Safety check valve to enclose the vacuum in case of a pump failure.
- Control and monitoring software with on-screen GUI.
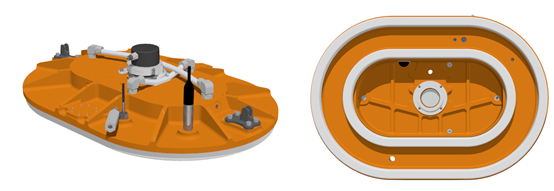
The cofferdam is installed by one of our M-ROVs with pinpoint accuracy.
To further increase the safety of the welders inside the hull, the M-ROV remains in place and holds the cofferdam during the repair. This means that the magnetic force of the M-ROV supplements the vacuum force, while the M-ROV can intervene immediately if necessary.
When the repair is finished the cofferdam is removed and retained to deck by the M-ROV.
Operational Steps:
- M-ROV dives with cameras, hull cleaning tool, grinder tool and the cofferdam.
- Cleaning the area from marine growth and locating the crack.
- M-ROV removes the paint along the crack by its grinder tool.
- M-ROV installs the cofferdam.
- Vacuum is established and water is drained from the vacuum chamber
- Integration test by shutting down the vacuum pump.
- Welders repair the crack.
- NDT of the repair weld.
- M-ROV removes the cofferdam
- Wet side inspection of the repair by the M-ROV`s cameras.
- M-ROV returns to deck.
We are proud that our solution has been used successfully by Equinor. During three offshore campaigns between 2018 and 2020, a significant number of cracks have been repaired. The campaigns have been conducted during harsh weather in the Norwegian Sea, working at a range from -9 to -1m depth.
Remotion has several cofferdams and M-ROV systems available for short notice mobilization Worldwide.